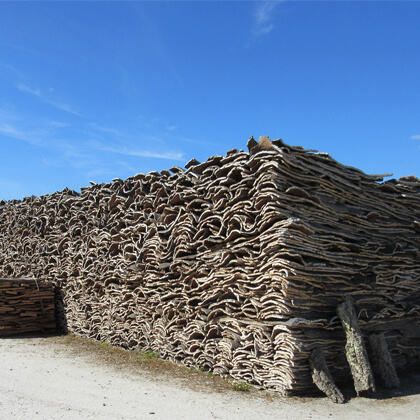
The rest
The boards are laid flat in the open air for 6 months to release their sap and moisture content.
The cork oak, or Quercus Suber, is a unique tree species. Indeed, it is harvested for its bark (which provides the cork) that has the ability to regenerate once extracted.
Its bark is collected directly from the trunk every 9 years at the earliest. Not a single tree is felled to harvest cork, it is one of the most environmentally friendly harvesting processes in the world.
This job requires considerable skill: even the hatchets are designed specifically for this purpose. This ancestral process is carried out by experts called “descortiçadores”. They can harvest nearly 600 kg of cork per day.
This results in an industry that is unique in the world, using an environmentally sustainable process that blends centuries-old tradition with the most modern practices.
Harvesting the cork is the first step which consists in removing the first bark from the tree.
This debarking operation is performed during the most active phase of cork bark growth, which starts in mid-May or early June and continues until the last days of August.
It is an ancestral process carried out by a specialist, the “descortiçador”. This task requires a great amount of dexterity and experience in order not to damage the tree, which makes it the best paid agricultural work in the world!
The first debarking is only performed after the cork oak reaches 25 to 30 years of age, when its trunk gets to 70 cm in circumference. This cork is called “male cork” (or “virgin cork”). It has an irregular and very hard structure, devoid of elasticity, impossible to handle and work with. It will be used to make insulation material for floors and walls.
The second debarking will take place nine years after. We will obtain a material whose structure is still irregular, less hard but of average quality, which is not yet able to provide a high-quality fabric.
It will be necessary to wait until the next harvesting (nine years later), to obtain cork that has the adequate properties.
From then on, the cork meets the quality requirements to be used in the manufacture of our (vegan) fabric. Therefore, it takes 43 to 48 years to obtain high-quality cork called “reproduction cork”.
Starting from this phase and at regular intervals of 9 years, the cork oak is ready to supply quality cork for about a century and a half, which amounts to an average of 16 bark harvests throughout its life.
The “descortiçador” cuts into the bark with an hatche, using the natural cracks in the wood in a vertical position to delineate the future boards.
Then he separates the cork board by inserting the edge of the hatche between the strip (the inside of the board) and the inner bark (the layer underneath the bark covering the wood of the trunk). Then, using the hatche, he performs a twisting movement between the trunk and the cork board that is to be extracted.
He now makes a horizontal cut to define the cork board remaining on the tree and the one to be removed. This is the most delicate operation performed on the tree as great care must be taken not to damage it.
The board is carefully removed from the tree to avoid breakage as much as possible. The bigger it is, the more valuable it is ! The dexterity and experience of the “descortiçador” determine the success in obtaining a beautiful board without cracks.
To complete the debarking process, the “descortiçador” paints a large number in white on each tree indicating the last date of its exploitation.
The boards are laid flat in the open air for 6 months to release their sap and moisture content.
Boiling the boards is one of the most important steps in the cork preparation phase.
The boards are sinked into boiling water for 1 hour with the aims of disinfecting and cleaning them, extracting water-soluble substances, increasing their thickness thus reducing their density, making them smoother, softer and more elastic.
During this process, cork volume increases by 20%.
After the boiling process, the boards undergo a stabilization period of two to four weeks.
The purpose of this phase is to smooth out the cork and allow it to rest. It will then reach the right consistency and a moisture content ranging between 12 and 15%.
The boards are examined very carefully (with the naked eye or optical sorting machines) to separate them into 2 categories:
– those with a good appearance and thickness
– and those with minor defects which will then be turned into granules.
Even the boards with flaws will be used to make granules. The cork never goes to waste!
The cork fabric is made from thin cork sheets cut straight from the boards or from cork blocks.
A block of cork is obtained by collecting defective boards and by-products such as those resulting from cork stopper production.
The gaps created during the tubing phase are also collected and turned into cork granules. These granules are then agglutinated through a process using pressure and heat.
The thin cork sheets are glued with water-based adhesive to a fabric backing.
The thin cork strips are glued with water-based adhesive to a fabric backing. They are placed next to each other very carefully, by hand, to create a patchwork.
For a better finish, the surface is also manually polished.
A dye consisting of a mixture of surfactants, pigments, additives and organic solvents is applied by hand to the fabric (as if painting a canvas).
The dyeing stage may possibly come before the gluing stage during the manufacture of the cork blocks. Before forming the cork blocks, the granules can also be dyed with pigments of different colours which will create beautiful textures as they agglomerate.
The drying time of the dye is quite fast, it takes few hours.
This still manual process ends with the application of a paraffin and silicone-based protective finish in order to maintain the intrinsic moisture content of the cork, the brightness of the colours and its impermeability.
Les planches sont stockées 6 mois à plat à l’air libre libérant ainsi leur teneur en sève et en humidité.
Le bouillage des planches est l’une des étapes les plus importantes de la phase de préparation du liège. Les planches sont plongées en eau propre en ébullition pendant 1h. L’objectif étant de les désinfecter et de les nettoyer pour en extraire les substances hydrosolubles. Au cours de ce processus l’épaisseur du liège augmente de 20% et les planches deviennent plus lisses, plus souples et élastiques.
Après l’opération de bouillage les planches sont soumises à une période de stabilisation allant entre deux à quatre semaines. Cette période sert à aplanir le liège et le laisse se reposer. Il acquerra ensuite la consistance adéquate et une humidité comprise entre 12 et 15%.
Les planches sont passées au peigne fin (œil nu où par des machines de tri optique) pour être séparées en 2 catégories :
– Celles présentant un bel aspect et une bonne épaisseur
– Celles ayant des défauts mineurs qui seront par la suite transformées en granulés.
Même les planches présentant un défaut seront utilisées pour la fabrication de granulés. Le liège n’est jamais gaspillé !
Le tissu liège est réalisé à partir de fines feuilles de liège découpées à même les planches ou à partir de blocs de liège. Un bloc de liège est obtenu par récupération des planches défectueuses et des sous-produits par exemple ceux issus de la fabrication des bouchons en liège. On récupère les interstices créés durant la phase de tubage en les transformant en granulés de liège. Ces granulés sont agglutinés entre eux au moyen d’un processus utilisant la pression et la chaleur.
Les fines feuilles de liège minces sont collées par adhésif à base d’eau sur un support en tissu. Elles sont placées les unes à côté des autres très minutieusement, à la main, afin de former un patchwork. Pour un meilleur rendu la surface est poncée également manuellement.
Une teinture constituée d’un mélange de tensioactifs, pigments, additifs et solvants organiques est appliquée à la main sur le tissu (comme si l’on peignait une toile). L’étape de la coloration peut éventuellement précéder l’étape du collage lors de la fabrication des blocs de liège. Avant de former les blocs de liège, les granulés peuvent également être colorés avec des pigments de couleurs différentes qui, en s’agglomérant entre eux, formeront de jolies textures.
Ce processus encore manuel se termine par l’application d’une finition protectrice à base de paraffine et silicone afin de maintenir le taux d’humidité intrinsèque du liège, la vivacité des couleurs et son imperméabilité.
Les planches sont stockées 6 mois à plat à l’air libre libérant ainsi leur teneur en sève et en humidité.
Le bouillage des planches est l’une des étapes les plus importantes de la phase de préparation du liège. Les planches sont plongées en eau propre en ébullition pendant 1h. L’objectif étant de les désinfecter et de les nettoyer pour en extraire les substances hydrosolubles. Au cours de ce processus l’épaisseur du liège augmente de 20% et les planches deviennent plus lisses, plus souples et élastiques.
Après l’opération de bouillage les planches sont soumises à une période de stabilisation allant entre deux à quatre semaines. Cette période sert à aplanir le liège et le laisse se reposer. Il acquerra ensuite la consistance adéquate et une humidité comprise entre 12 et 15%.
Les planches sont passées au peigne fin (œil nu où par des machines de tri optique) pour être séparées en 2 catégories :
– Celles présentant un bel aspect et une bonne épaisseur
– Celles ayant des défauts mineurs qui seront par la suite transformées en granulés.
Même les planches présentant un défaut seront utilisées pour la fabrication de granulés. Le liège n’est jamais gaspillé !
Le tissu liège est réalisé à partir de fines feuilles de liège découpées à même les planches ou à partir de blocs de liège. Un bloc de liège est obtenu par récupération des planches défectueuses et des sous-produits par exemple ceux issus de la fabrication des bouchons en liège. On récupère les interstices créés durant la phase de tubage en les transformant en granulés de liège. Ces granulés sont agglutinés entre eux au moyen d’un processus utilisant la pression et la chaleur.
Les fines feuilles de liège minces sont collées par adhésif à base d’eau sur un support en tissu. Elles sont placées les unes à côté des autres très minutieusement, à la main, afin de former un patchwork. Pour un meilleur rendu la surface est poncée également manuellement.
Une teinture constituée d’un mélange de tensioactifs, pigments, additifs et solvants organiques est appliquée à la main sur le tissu (comme si l’on peignait une toile).
L’étape de la coloration peut éventuellement précéder l’étape du collage lors de la fabrication des blocs de liège. Avant de former les blocs de liège, les granulés peuvent également être colorés avec des pigments de couleurs différentes qui, en s’agglomérant entre eux, formeront de jolies textures.
Ce processus encore manuel se termine par l’application d’une finition protectrice à base de paraffine et silicone afin de maintenir le taux d’humidité intrinsèque du liège, la vivacité des couleurs et son imperméabilité.
Our cork fabrics are embroidered and sewn by hand using a standard sewing machine and ordinary thread.
This vegan fabric is also very easy to cut, which enable us to give free rein to our imagination and creativity by layering different shapes and colours!
Cookie | Type | Duration | Description |
---|---|---|---|
Cookies related to social networks and advertising | Social media cookies enable you to log in to your social networks and share content from our website through those social networks. Advertising cookies (or third-party cookies) collect information in order to provide you with advertising content relevant to your interests. In some cases, these cookies use your personal data. They do not store personal data directly, but they are based on the unique identification of your browser and Internet device. If you disable these cookies, advertisements will still be displayed during your Internet browsing but they will not take your interests into account and will therefore be less relevant. Your advertisement will be less targeted. | ||
Functional Cookies | 13 | These cookies enable the website to provide enhanced functionality and personalisation. These cookies allow us to provide you recommendations of products, content that match your expectations and preferences. By accepting these cookies, you are opting for an enriched and personalised experience. If you do not allow these cookies then some or all of these services may not function properly. | |
Statistical analysis cookies | 13 | These cookies allow us to improve the site’s functionality by tracking usage on the website. In some cases these cookies can improve the speed with which we can process your request as they allow us to remember site preferences that you’ve selected. These cookies are used to measure and analyse our website audience (visitor volume, pages viewed, average browsing time, etc.). They help us to know which pages are the most and least popular and see how visitors move around the site. All information these cookies collect is aggregated and therefore anonymous. If you do not allow these cookies we will not know when you have visited our site, and will not be able to monitor its performance. De-selecting these cookies may result in poorly-tailored recommendations and slow site performance. |